Home »
Blog » Page 59
Improvement Insights Blog
Latest Posts
Dr. Richard J. Albin, creator of the PSA test for prostate cancer, says that the devastating consequences treatments including surgery and radiation therapy caused:
- 5,000 deaths soon after surgery
- up to 70,000 serious complications
- 50% had persistent blood in their semen
- up to 300,000 suffered impotence, incontinence or both.
He now calls the widespread use of the PSA test a “Public Health Disaster.” As a result of these findings, the U.S. Preventive Services Task Force will recommend that healthy men no longer receive PSA testing.
Unnecessary tests and treatments of all kinds are estimated to cost $250 Billion in the U.S.
Continue Reading "PSA Test – a Public Health Disaster"
Posted by Jay Arthur in Lean, Service, Six Sigma.
Last weekend, a United Airlines computer glitch delayed and cancelled flights. Even the redundant backup system didn’t work properly.
In a world increasingly dependent on computers and software, IT has been steadfastly resistant to the methods of Six Sigma. While Agile (Lean) programming methods have accelerated software development, mistakes, errors, hitches and glitches continue to plague worldwide productivity. Hardly a day goes by that my PC doesn’t try to install an “upgrade” to some piece of software: Windows, Java, etc.
Sadly, most software escapes rather than releases. Maybe it’s time to start using Six Sigma to optimize delivered software.
Continue Reading "No Fly Zone"
Posted by Jay Arthur in Jay Arthur Blog.
Seth Godin’s blog brought this data to my attention: http://www.nextbigfuture.com/2011/03/deaths-per-twh-by-energy-source.html.
There’s lots of ways to display it, but I thought it would be fun to look at as Pareto charts.
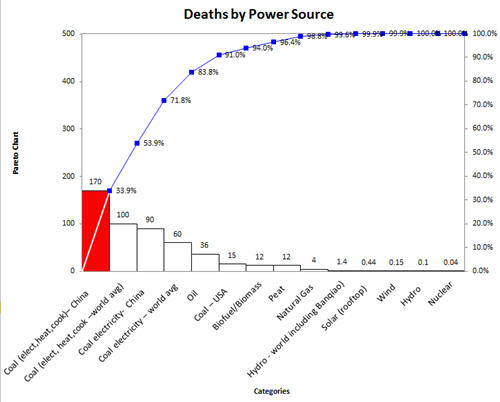
Deaths from nuclear power are small compared to the power produced. Coal and oil are still the heavy hitters in the mortality department.
Continue Reading "Deaths by Power Source Data"
Posted by Jay Arthur in QI Macros.
The March 2011 Wired magazine article identifies a new trend in manufacturing: insourcing. An MFG.com survey found that 19% of companies had brought all or part of their manufacturing back to North America. US manufacturing added 136,000 jobs in 2010, the first increase since 1997.
While many small to medium sized businesses moved their manufacturing to China in the early part of the last decade, many are finding benefits from moving production back to the USA:
- Rising labor costs in China are making the USA more cost competitive. China wages more than doubled between 2002-2008.
- Sheer distance “remains an intractable problem.”
Continue Reading "Insourcing Manufacturing"
Posted by Jay Arthur in Six Sigma.
Last week, Toyota unveiled it’s multimillion dollar system for gather repair reports, complaints and safety concerns from dealerships, internet sites and other sources into one system and mine that data for problems beyond the doors of the factory. The WSJ reported that EVP Shinichi Sasaki said that Toyota had succumbed to ‘Big Company Disease’.
It happens. Big or small, companies shift their focus to bottom-line benefits or growth and drop the ball on quality. But, as I’ve predicted for awhile, Toyota’s quality culture is repairing itself and resuming the quest for quality; now on a global basis.
What are you doing to monitor your quality on a global basis?
Continue Reading "Toyota’s Global Data Mining"
Posted by Jay Arthur in Lean, Manufacturing, Six Sigma.
Good insights.
http://www.shmula.com/marc-onetto-lean-six-sigma-at-amazon/8042/
Continue Reading "Amazon’s use of Lean Manufacturing"
Posted by Jay Arthur in Lean.
Use a histogram to determine the distribution of measurable data and the capability (i.e., the level of performance the customers can consistently expect) of the process. Process capability is determined using your data and the customer’s upper specification (USL) and lower specification limits (LSL).
Its easy to create a histogram in Excel using the QI Macros. See
http://www.youtube.com/user/QIMacros#p/a/u/2/tqlFKtmAxbU
Continue Reading "Create a Histogram in Excel Using the QI Macros"
Posted by Jay Arthur in QI Macros.
Control Charts show your data as a line graph with average and sigma lines to determine stability. The average and sigma lines are calculated from your data. It’s easy to create a control chart in excel using the QI Macros. See http://www.youtube.com/watch?v=5TVKz4OQTp0
Continue Reading "Use Control Charts to Determine Process Stability"
Posted by Jay Arthur in QI Macros.
Last week, we exhibited at the Magnet conference for nursing quality. Every healthcare quality conference has posters about improvement projects: Magnet, NAHQ, and IHI. What struck me about these posters was the shortage of quality tools like control charts, pareto charts and fishbone diagrams. Those posters using charts often used the incorrect type of chart for the data.
Here’s an example. This chart has so many lines on it, how can you tell what story they are trying to tell?

Here’s an example using a bar chart (instead of a line graph) and the dates are in reverse order:

Here’s another bar chart with the dates in the correct order, but again, time series charts like this one should be shown as a line, run or control chart.
Continue Reading "Magnet Improvement Posters"
Posted by Jay Arthur in Six Sigma.
BusinessWeek Sept. 20-26, 2010 calls UPS managers “efficiency freaks.” USP began equiping trucks with sensors for everything from brake pad wear to engine efficiencies. This data has helped reduce gas consumption by 25 gallons per year per truck.
Doesn’t sound like much until you realize that UPS has an estimated 95,000 vehicles which means saving almost 2,500,000 gallons per year. Multiply that by $2.50/gallon to get a $6+ million dollar savings. And it makes for a greener planet.
Maybe we could all benefit from more “efficiency freaks.”
Continue Reading "UPS Efficiency Freaks"
Posted by Jay Arthur in Service, Six Sigma.